Die Anforderungen an Montagesysteme in der Photovoltaik sind vielfältig, nicht nur aufgrund der verschiedenen Anlagentypen wie Freifläche oder Dach. Statische Auslegung und konstruktive Gestaltung sowie die Dauerhaftigkeit sind einige der Kriterien, die in die Planung eines Untergestells einfließen.
Verzinkung im Stück oder am Band
Der hohe Kostendruck zwingt die Industrie im Sinne einer ganzheitlichen Betrachtung, qualitativ hochwertige, dauerhafte und wettbewerbsfähige Anlagen zu entwickeln. Der Grundwerkstoff Stahl schafft diesen Spagat, insbesondere wenn er mit einem lang wirkenden und wartungsfreien Schutz gegen Korrosion und mechanische Belastungen versehen ist.
Zink als Schutzschicht bewährt sich in verschiedenen Anwendungen bereits seit Jahrhunderten. Auch bei Montagegestellen für die Photovoltaikbranche liefert verzinkter Stahl ein solides Fundament.
Technologisch unterscheidet man zwischen dem Verfahren der Stückverzinkung und der kontinuierlichen Bandverzinkung. Vereinfacht gesagt, werden bei der traditionellen Stückverzinkung bereits fertig geformte Komponenten in ein Zinkbad getaucht, während beim kontinuierlichen Verfahren das Zink auf den noch flachen Bandstahl aufgebracht wird und die Einformung zum Profil erst nach der Verzinkung erfolgt. Der Stahlverarbeiter Wuppermann in Leverkusen hat bereits 1989 eine damals neue Technologie zum Verzinken von warmgewalztem Bandstahl entwickelt und damit einen Grundstein für das heutige, kontinuierliche Verfahren gelegt.
Vorteile der Bandverzinkung
Das kontinuierliche Verfahren bringt einige Vorteile mit sich. Die Zinkschicht wird innerhalb weniger Augenblicke auf den vorgewärmten Bandstahl aufgebracht.
Die Zinkschichtdicke kann über sogenannte „Air Knives“ stufenlos von 50 Gramm pro Quadratmeter auf bis zu 1.200 Gramm pro Quadratmeter eingestellt werden und ist unabhängig von der Dicke des Stahlbandes.
Das heißt, dass auch sehr dünner Stahl mit sehr hohen Zinkschichtdicken versehen werden und in besonders rauen Umgebungen zum Einsatz kommen kann. Dieser Zusammenhang wird später noch einmal vertieft.
Durch das sehr rasche Applizieren des Zinks wird eine sehr homogene und bis zum Stahlgrund durchgehende Phase aus Reinzink ausgebildet. Durch einen äußerst geringen Anteil von Aluminium im Zinkbad entsteht ein Haftverbund mit dem Stahl. Diese „Klebeschicht“ unterbindet gleichzeitig die Bildung der unerwünschten Zink-Eisen-Legierung.
Nachteile beim Stückverzinken
Beim Stückverzinken muss sich die Zinkschicht über einen längeren Zeitraum aufbauen, also aufwachsen. Dadurch entstehen mehrere Phasen mit unterschiedlichen Anteilen an Eisen und von Zink.
Nur ganz an der Oberfläche bildet sich eine sehr dünne Reinzinkphase aus. Mikrorisse durchziehen die Phasen und beschleunigen Oxidation und damit Korrosion. Produktionsbedingt könnte es bei der Stückverzinkung zu oberflächennahen Einschlüssen von Blei kommen, die beim Bewitterungsprozess in die Umwelt eingetragen werden.
Aktiver Schutz der Kathode
Gegen kontinuierlich verzinkten Stahl wird häufig das Argument vorgebracht, dass im weiteren Fertigungsprozess vorgenommene Schnitte oder Stanzungen unbeschichtet und damit ungeschützt der Witterung ausgesetzt sind.
Diese Aussage wird durch eine sehr positive Eigenschaft von Zink entkräftet. Zink opfert sich als unedleres Metall und schützt durch einen elektrochemischen Wirkprozess den Stahl bei natürlicher Bewitterung gegen Rotrostbildung. Man spricht hier von aktivem Korrosionsschutz oder Kathodenschutz.
Dennoch, speziell bei Rammprofilen ist die Empfehlung von längsverzinkten Kanten angebracht, da gerade im Boden-Luft-Übergang ein erhöhtes Risiko für die Bildung von Korrosionsprodukten an unbeschichteten Stellen besteht.
Zuspruch zu Zink-Magnesium wächst
Den Service einer verzinkten Längskante liefert die Bandverzinkungsanlage der Wuppermann Austria in Judenburg bis zu einer Bandbreite von maximal 410 Millimetern.
Neben der klassischen Beschichtung mit Reinzink sichert sich seit Jahren eine Legierung aus Zink, Magnesium und Aluminium (ZM) eine immer größer werdende Fangemeinde in der Solarindustrie. Diese Legierung wird ausschließlich in einem kontinuierlichen Verfahren auf den Stahl aufgebracht. Unterschiedliche Anteile von Magnesium (Mg) und Aluminium (Al) wirken sich unterschiedlich auf die Eigenschaften der Legierung aus und bestimmen letztendlich den Anwendungsbereich.
Für die teilweise sehr heterogenen Anforderungen in der Photovoltaikbranche hat sich eine Legierung mit einem etwas höheren Anteil von Magnesium und Aluminium (jeweils etwa drei Prozent) als gegen Korrosion besonders widerstandsfähig bewährt.
Kategorien sichern Planungen ab
Standardisierte Laboruntersuchungen und aus der Praxis erworbene Erkenntnisse bescheinigen dieser ZM-Legierung ganz allgemein gesprochen eine wesentlich höhere Korrosionsbeständigkeit als Reinzink.
Die Beständigkeit von Schichtdicken ist je nach Belastung der Luft regional sehr unterschiedlich. Für die sogenannte atmosphärische Korrosion wurde eine Klassifizierung der Umweltbedingungen in Korrosivitätskategorien vorgenommen, die in der EN ISO 12944-2 dargestellt sind.
Einen Schritt weiter geht die deutsche Norm DIN 55634-1. Dieser Standard setzt erstmals die zu erwartende Schutzdauer unterschiedlicher kontinuierlich aufgebrachter Z- und ZM-Schichten mit den verschiedenen Korrosivitätskategorien in Beziehung.
Dem Anwender wird ein Instrument in die Hand gegeben, das eine normbasierte Bestimmung der Dauerhaftigkeit und damit hohe Planungssicherheit ermöglicht. Für die Kategorisierung wurden die maximalen Abtragungsraten herangezogen, sodass sich eine konservative Abschätzung über die wartungsfreie Standdauer treffen lässt.
Aus der Tabelle ergibt sich die Aussage, dass unter gleichen Umgebungsbedingungen zum Beispiel eine Z600-Schicht durch eine ZM300-Schicht substituiert werden kann, ohne an Korrosionsschutz zu verlieren. Neben reduziertem Ressourceneinsatz bedeutet das auch reduzierte Kosten.
Sehr hohe Auflagen möglich
Die DIN 55634-1 berücksichtigt Auflagen bis zu 600 Gramm je Quadratmeter bei Reinzink und 430 Gramm pro Quadratmeter bei ZM. Doch mit diesen Werten sind die Produktionsmöglichkeiten inzwischen längst nicht ausgeschöpft. In der Bandverzinkungsanlage von Wuppermann im steirischen Judenburg werden Auflagen von bis zu 1.200 Gramm pro Quadratmeter in Reinzink und 1.000 Gramm pro Quadratmeter in Zink-Magnesium (Wuppermann Zink-Magnesium, kurz: Wzm) gefertigt.
Die hohen Z- und ZM-Auflagen eröffnen neue Möglichkeiten für sehr raue Umgebungsbedingungen oder Rammprofile. Auch relativ neue Bauformen wie Floating PV oder Agro PV stellen erhöhte Anforderungen an die Korrosionsbeständigkeit. Dies ist beispielsweise der Fall bei schwimmenden Anlagen, die einem höheren Gehalt an Feuchte und Salz in der Umgebungsluft ausgesetzt sind, oder bei landwirtschaftlichen Flächen, bei denen Düngemittel eingesetzt wird.
Ebenso werden durch unterschiedliche Vornutzung belastete Flächen zur Erzeugung erneuerbarer Energie herangezogen und entsprechend aufgewertet. Speziell für diese Einsätze ist Stahl, der mit hohen Zink- oder Zink-Magnesium-Auflagen beschichtet ist, beispielsweise Wuppermann Zink-Magnesium, prädestiniert.
Längere Nutzungsdauer möglich
Parallel dazu sind die Hersteller mit Forderungen nach immer länger währenden Nutzungsdauern für das Montagegestell konfrontiert. Mit diesen Produkten können diese erfüllt werden, sofern die konkreten Projektbedingungen nicht komplett aus dem Rahmen fallen.
Welche Schutzdauern sich für kontinuierlich beschichtetes Material von Wuppermann im Hinblick auf atmosphärische Korrosion ergeben, wird durch eine Zulassung durch das Deutsche Institut für Bautechnik (DIBt) verdeutlicht. Die Werte ergeben sich aus konservativen Berechnungen anhand von Abtragungsraten, die in Versuchen ermittelt wurden.
Komplexe Schichten für Rammprofile
Wie verhält es sich im Gegensatz dazu mit Rammprofilen, also mit Komponenten, die in den Boden getrieben werden und für die die oben genannten Beurteilungskriterien nicht herangezogen werden können?
Die Beurteilung, um das richtige Beschichtungssystem für Rammprofile empfehlen zu können, ist mindestens eine Größenordnung komplexer. Hier befinden sich unterschiedliche Parameter des „Ökosystems Photovoltaikanlage“ in Wechselwirkung. Dazu gehören die Eigenschaften der Böden, der metallischen Werkstoffe und deren Schutzschicht sowie auch die Umgebungsbedingungen und Eigenschaften der Anlage selbst.
In der Norm EN ISO 12944-2 wird unter anderem auf die Korrosionsbelastungen für Stahl durch das Erdreich hingewiesen. Die Vorschrift geht auch auf die Kategorie „lm3“ für erdreichberührte Stahlbauten ein.
Gutachten für Rammfundamente
Weiterhin sollte die Norm EN 12501 Beachtung finden. Hier werden unter anderem Faktoren beschrieben, die die Korrosionsbelastung erdüberdeckter metallischer Werkstoffe beeinflussen. Auch das Vorgehen zur Beurteilung der Korrosionsbelastung im Boden von der Voruntersuchung bis zur Entnahme von Bodenproben hat dieser Standard zum Thema.
Im Sinne der Investoren werden Solarprojekte in der Regel von Bodengutachtern begleitet, die mit unterschiedlichen Methoden die Beschaffenheit des Untergrunds bestimmen. Wesentliche Faktorenfür die Dauerhaftigkeit von mit Zink- oder Zink-Magnesium beschichteten Rammpfosten sind beispielhaft die Bodenklasse, der pH-Wert, der spezifische Bodenwiderstand, der Feuchtegehalt und die Lage des Grundwassers im Boden. Klassifizierungen zu diesen Einflüssen finden sich in den beiden Normen DIN 18300 und DIN 50929-3. Aussagefähige Bodengutachten liefern Bewertungszahlen, die auf den Grad der Korrosionsbelastung schließen lassen.
Kein Projekt gleicht dem anderen
Speziell bei der Empfehlung von Schutzschichtdicken für Rammprofile gilt: Kein Projekt gleicht dem anderen. Deshalb sind gerade bei dieser Beurteilung die zeitgerechte Einbindung der Korrosionsschutzexperten des Gestelllieferanten und eine offene Kommunikation mit Planern und Gutachtern zielführend. Auf diese Weise werden Lösungen gefunden, die maßgeschneidert zu den Anforderungen des Projektes passen.
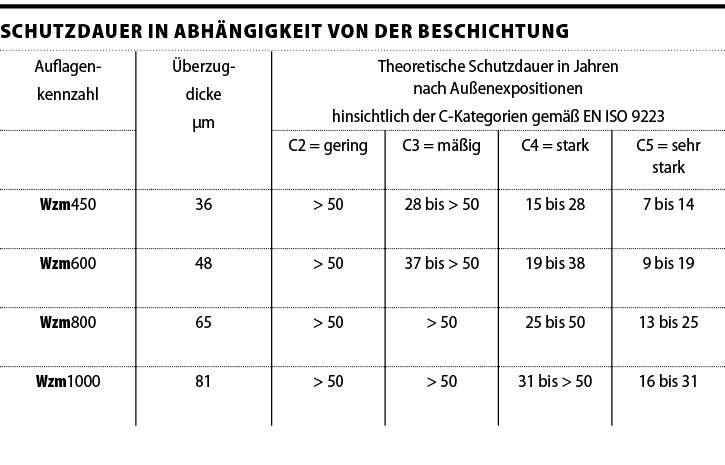
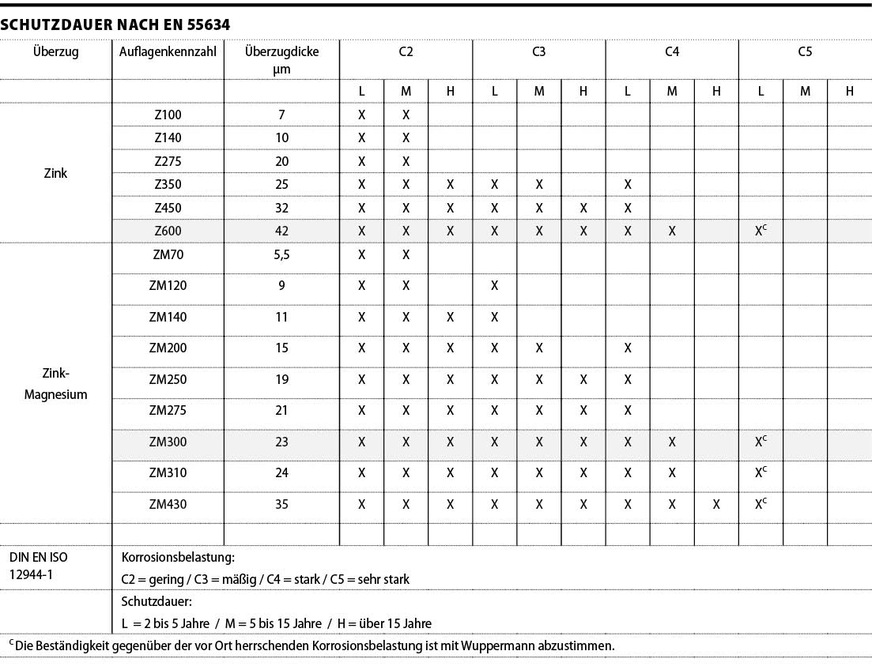
Schletter Gruppe/Dörken MKS
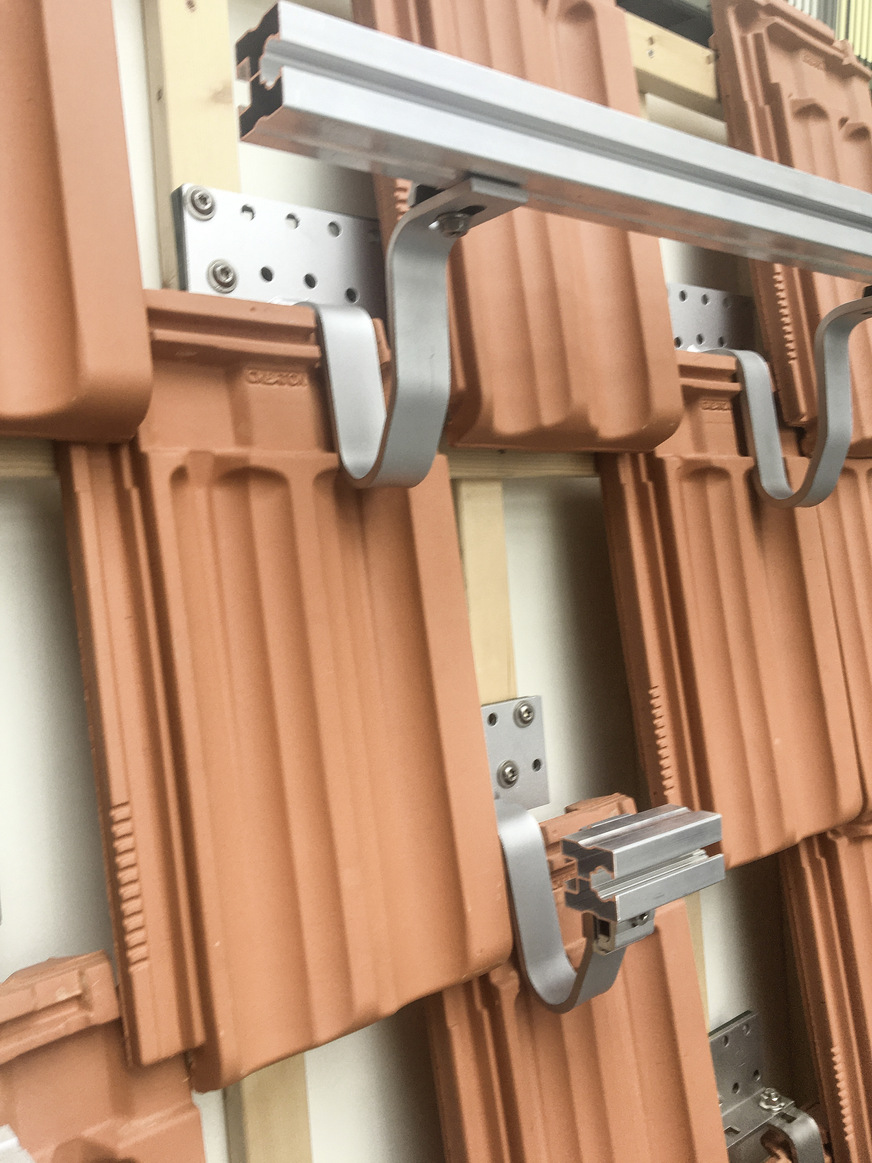
Foto: Schletter Group/Doerken MKS
Dachhaken aus hochfestem Stahl mit Zinklamellensystem
Die Schletter Gruppe setzt bei der Beschichtung der neuesten Dachhaken für Solaranlagen auf eine hochleistungsfähige Zinklamellenbeschichtung von Dörken MKS.
Speziell für die Installation von Solaranlagen auf Ziegeldächern mit Unterkonstruktionen aus Holz hat Schletter eine neue Generation von Dachhaken aus der hochfesten Stahlsorte S700MC auf den Markt gebracht. Diese verfügen über die European Technical Approval (ETA).
Im Vergleich zu den Vorgängermodellen oder zu herkömmlichen Edelstahlhaken gewährleisten die neuen Dachhaken eine deutlich höhere Tragfähigkeit, mechanische Festigkeit, Stabilität und Standsicherheit – wodurch auch die Anzahl der Befestigungspunkte pro Kilowatt Solarleistung reduziert werden kann.
Für eine dauerhafte Korrosionsbeständigkeit auch bei härtesten Witterungsbedingungen sorgt ein anforderungsgerechtes Zinklamellensystem von Dörken MKS. Während der Basecoat einen zuverlässigen kathodischen Korrosionsschutz sichert, ermöglicht der speziell darauf abgestimmte Topcoat eine hervorragende Witterungsbeständigkeit. So werden die hohen Qualitätsanforderungen der Schletter Gruppe erfüllt.