Weg von Cobalt und Nickel: Das ist ein klares Ziel der Batterieforschung. Denn die Materialien gelten als teure und kritische Elemente. Natrium-Ionen-Akkus hingegen nutzen eine Kathode aus Preußischweiß oder auch Preußischblau. Das ist ein Komplex auf Eisenbasis, der günstig ist und zudem in großer Menge zur Verfügung steht. Genau dieses Preußischweiß will die junge Firma Litona aus Karlsruhe künftig in Batteriezellen einsetzen. Das Material basiert im Wesentlichen auf Natrium, Eisen und Mangan.
Litona will Natrium für die Kathode nutzen
Das Start-up selbst entstammt dem Karlsruher Institut für Technologie, kurz KIT, und will diese Batterien nun im industriellen Maßstab herstellen. „Als Energiespeichermaterial kann es an der Kathode, also dem Pluspol einer Natrium-Ionen-Batterie, eingesetzt werden“, erklärt Sebastian Büchele. Batterien sind sein Element, könnte man sagen.
Büchele forscht am Institut für Angewandte Materialien des KIT und hat die Firma Litona gegründet. Die Natriumbatterien sind günstig und alle enthaltenen Rohstoffe breit verfügbar. „Ich bin davon überzeugt, dass wir sie bald massenhaft in Elektrofahrzeugen und Netzspeichern verwenden können“, meint er. Die Frage sei allerdings, wer sie produzieren soll. Hier steht die europäische Industrie vor einem großen Problem. „Derzeit ist es selbst für Forschungseinrichtungen schwierig, sich Preußischweiß in ausreichenden Mengen zu beschaffen“, weiß auch der Wissenschaftler.
Fertigung von Preußischweiß
Kaum ein Unternehmen in Europa stellt Preußischweiß zurzeit her. Dadurch würden Forschung und Transfer der Natrium-Ionen-Technologie aktuell extrem ausgebremst, berichtet der junge Wissenschaftler. Da auch Büchele an der Natrium-Ionen-Technologie forschen wollte, beschloss er, Preußischweiß selbst zu synthetisieren. Das erste Ergebnis kann sich sehen lassen: So entstand am KIT nicht nur ein hochwertiges Kathodenmaterial, sondern auch ein innovatives Verfahren für dessen Herstellung.
Nun sollen die Fertigungsmengen steigen. Deshalb gründete er gemeinsam mit dem Chemiker Tom Bötticher das eigene Start-up. „Bei Wettbewerbern gab es Probleme bei der Skalierung der Produktion von Preußischweiß-Analoga“, sagt Büchele. Analoga sind chemische Verbindungen mit gleicher biologischer Wirkung. Er ist aber optimistisch, dass seine Firma das Problem gelöst hat.
Chance für die Industrie in der EU
Um die Skalierungsschritte zu validieren und das Material für den Einsatz in Batterien der nächsten Generation zu optimieren, nutzt Litona die Infrastruktur des KIT. Inzwischen arbeiten die beiden Gründer bereits am Aufbau einer eigenen Produktion. „Wir haben uns dabei bewusst für den Standort Deutschland entschieden“, betont Bötticher. Die Gründer glauben an das Potenzial einer europäischen Batterieproduktion.
Natrium-Ionen-Batterien gelten als aussichtsreiche Alternative zu Lithiumspeichern, zumindest für einige Anwendungen der Industrie. Die Vorteile: Natrium ist leicht verfügbar, kostengünstig und lässt sich gut recyceln. Aber es gibt auch Nachteile: Reines Natrium ist an sich sehr reaktiv. Bei Berührung beispielsweise mit Wasser kann es brennen oder explodieren. Jedoch ist Natrium weniger reaktionsfreudig als Lithium – und neigt kaum zur Dendritenbildung, die die Kurzschlussgefahr erhöht. Natriumbatterien können zudem unter bestimmten Bedingungen schneller geladen werden als Lithiumakkus. Und das wiederum könnte die Ladezeiten von Elektrofahrzeugen deutlich verkürzen – das ist ein wichtiger Punkt.
Forschung steckt noch in den Kinderschuhen
Im Vergleich zur Lithium-Ionen-Technologie steckt die Forschung jedoch noch in den Kinderschuhen. „Schon jetzt haben wir Energiedichten von 150 Wattstunden pro Kilogramm und sind somit nicht weit entfernt von LFP-Zellen“, sagt Sven Bauer, Chef und Gründer der BMZ Group. Das Potenzial sei also riesig und die anfänglichen Nachteile würden über die Jahre immer geringer. BMZ testet schon den mobilen Speicher Power2go mit Natrium-Ionen-Akkus und will künftig auch die Energiespeicherlösungen mit der neuen Technologie ausstatten. Aber wie immer kommt es dabei auf die konkreten Anforderungen des Kunden an. Durch die modulare Bauweise sei BMZ in der Lage, die Speicher zukünftig mit allen gängigen Zellchemien auszurüsten.
30 Prozent weniger Kosten auf Zellebene
Beim Systempreis für Speicher erwartet der Hersteller den größten Vorteil. Denn neben der hohen Verfügbarkeit von Natrium seien auch die weiteren Bestandteile wie Anode und Kathode einfacher und günstiger herzustellen. „So gehen wir davon aus, dass sich abhängig von der Nachfrage auch der Preis deutlich unter dem der LFP-Technologie bewegen wird. Konkret: mehr als 30 Prozent weniger Kosten auf Zellebene“, resümiert Bauer.
Der Hersteller muss sicherstellen, dass seine Speicher möglichst zukunftssicher sind. BMZ setzt deshalb zum einen auf eine modulare Bauweise und zum anderen auf seine eigenen Batteriemanagementsysteme (BMS). „Durch unsere Tochterunternehmen und die eigene Entwicklung sind wir in der Lage, als Systemanbieter am Markt zu agieren und sicherzustellen, dass alle gängigen Sicherheitsnormen und Anforderungen erfüllt werden“, erklärt Bauer. Durch die entsprechend hohe Wertschöpfungskette kann BMZ jederzeit gewährleisten, dass die Produkte entsprechend der neuen EU-Batterieverordnung hergestellt werden.
Varta initiiert Entise-Projekt
Das Forschungsprojekt Entise will die Natrium-Ionen-Technologie ebenfalls schnell in die Massenfertigung bringen. Das Kürzel steht für die „Entwicklung der Natrium-Ionen-Technologie für industriell skalierbare Energiespeicher“. Entise besteht aus einem Konsortium, das 15 Unternehmen und Hochschulen vereint. Der Bund steuerte rund 7,5 Millionen Euro Fördergelder bei.
Initiiert und koordiniert wird das Projekt von Varta aus Ellwangen. Erst im Januar hatte der Konzern seine Kapazitäten für Forschung und Entwicklung von Batterien ausgebaut. Im österreichischen Graz wurde ein neues Labor eingerichtet, mit einer Fläche von etwa 3.500 Quadratmetern – rund 50 Forscher sollen dort arbeiten.
Kleinserie und Praxistests sollen 2027 starten
Die Forscher wollen mit dem Entise-Projekt vor allem die Speicherkapazitäten der Kathode und Anode der neuen Technologie verbessern. Durch neue Materialien und verbesserte Beschichtungen der Elektroden soll die Zyklenstabilität steigen. Sie bezeichnet die Fähigkeit, die Ladeleistung der Zellen trotz vielfachen Be- und Entladens stabil zu halten. Im Ergebnis sollen belastbare Labormuster und Prototypen mit Rundzellen entstehen. Am Ende des Projekts Mitte 2027 soll es eine Kleinserie geben, die belastbare Praxistests in stationären Speichern und E-Autos meistert.
Bei den Lithium-Ionen-Batterien hatte Asien in den vergangenen Jahren die Nase vorn. Die Natrium-Ionen-Technologie bietet nun eine Riesenchance für einen Neuanfang in Europa. Litona-Gründer Büchele gibt sich deshalb betont kämpferisch: „Wir wollen dabei nicht nur zuschauen.“
https://www.litona-batteries.de
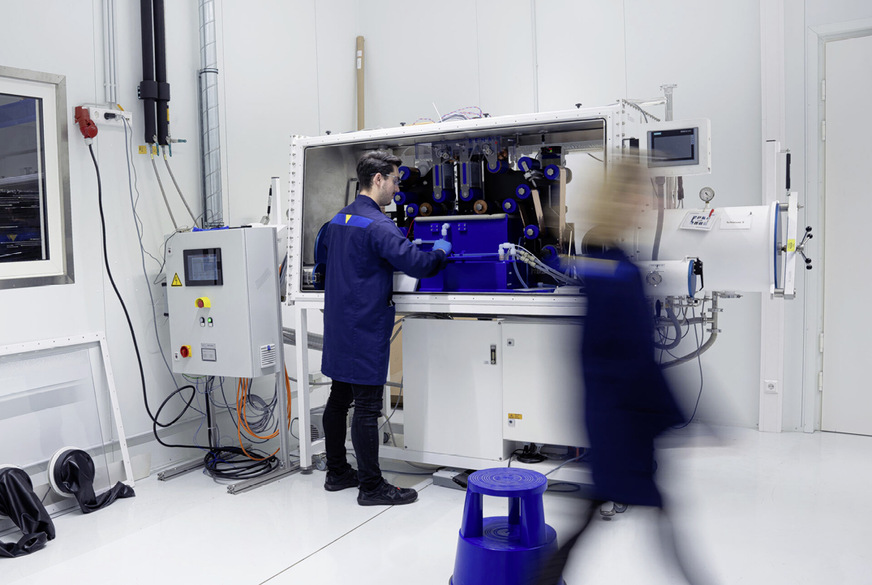
Foto: Varta
BMZ Group
Natrium-Ionen-Batterien: Serienproduktion soll 2025 starten
Die BMZ Group aus Karlstein legt die neue Baureihe Nate mit Natriumbatterien auf. Die Zellformate werden zylindrisch und prismatisch angeboten. Der Start der Serienproduktion wird Mitte 2025 erfolgen. Die BMZ Group wird ihr Portfolio damit um Natrium-Ionen-Batteriezellen erweitern. Erste Prototypen werden mit Zellformaten 21700 und 46130 getestet und zur Serienreife entwickelt. Weitere Zellformate sollen laut Hersteller folgen. Während spezifische Kundenprojekte bereits anlaufen, soll die Serienproduktion im Sommer 2025 starten.
Natrium-Ionen-Zellen gelten als besonders sicher, weil Natrium weniger reaktionsfreudig als Lithium ist und auch kaum zur Dendritenbildung (Kurzschlussgefahr) neigt. Hinzu kommen die höhere Verfügbarkeit und größere Umweltfreundlichkeit, weil auf seltene, toxische oder schwer zu gewinnende Materialien verzichtet wird. Die Nate Series wird entwickelt und vertrieben von der Terra E GmbH, einer Tochter der BMZ Group.
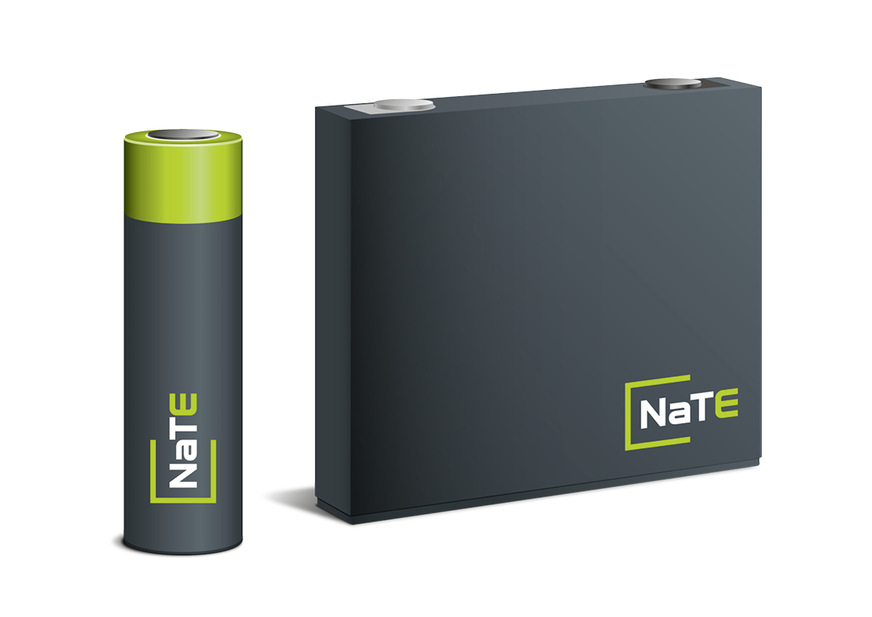
Foto: BMZ Group
Prolux Solutions
25 Projekte nutzen Redox-Flow-Speicher in der Kaskade
Im vergangenen Jahr wurden insgesamt 25 Kaskadierungsprojekte mit dem Redox-Flow-Speicher Storac realisiert oder stehen kurz vor der Fertigstellung. Die Kaskaden verbinden mehrere Speicher mit je sechs Kilowattstunden Kapazität. Anwender sind unter anderem Besitzer von Holzhäusern und öffentlichen Gebäuden wie Kindergärten und Schulen. Sie verbindet ein hohes Sicherheitsbedürfnis, das vom Flow-Speicher erfüllt wird, weil er die Brandlast im Gebäude nicht erhöht. Die aktuellen Projekte haben eine Kapazität von über 280 Kilowattstunden.
Bei Liegenschaften mit mehreren Gebäuden kann es sinnvoll sein, die Speicher auf verschiedene Gebäude zu verteilen, um das Leitungsnetz effizient zu nutzen. Durch das integrierte Energiemanagement des Speichers können dabei auch große Entfernungen überbrückt werden. „In einem unserer Projekte sind die Redox-Flow-Speicher 1,2 Kilometer voneinander entfernt“, sagt Johannes Häntzschel, Geschäftsbereichsleiter für die Sparte Battery Storage bei Prolux Solutions.
Das integrierte Energiemanagement vernetzt die Speicher nicht nur untereinander, sondern steuert auch weitere Komponenten wie Wärmepumpen. „Zudem ist die Kapazität jederzeit skalierbar, da es bei Redox-Flow so gut wie keine Alterungseffekte gibt“, sagt Häntzschel.
https://www.prolux-solutions.com
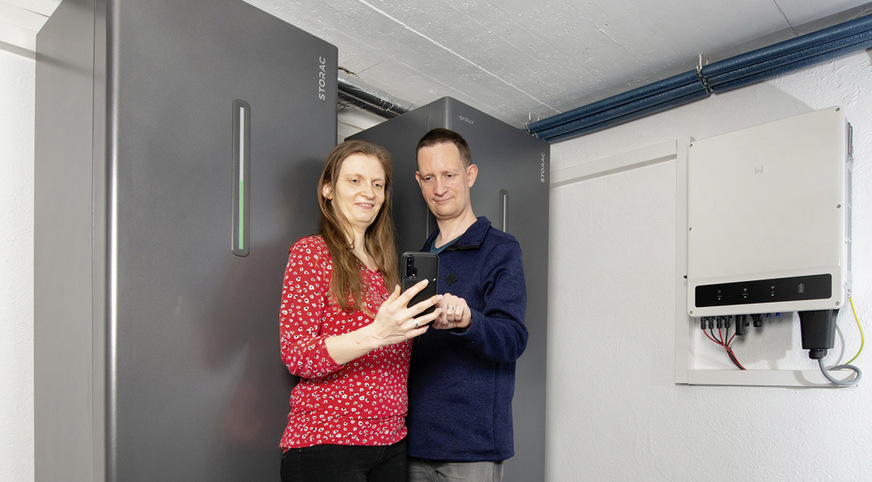
Foto: Prolux
TU Braunschweig
Circularlab will Lithiumzellen wiederverwenden
Die TU Braunschweig hat das sogenannte Circularlab eröffnet, um Lithiumzellen zu recyceln und in eine Kreislaufproduktion zu überführen. Denn die Zellfertigung nimmt eine Schlüsselfunktion in der Wertschöpfungskette der E-Mobilität ein. So macht die Batterie etwa 80 Prozent der Kosten des Antriebsstrangs aus.
Die Elektromobilität und die Energiewende brauchen also leistungsstarke, kostengünstige und umweltschonende Batteriezellen. Damit Lithium-Ionen-Batterien nachhaltig sind, müssen Produktionsausschuss und genutzte Batterien recycelt und die Materialien in einem geschlossenen Materialkreislauf gehalten werden. Herauszufinden, wie dies technisch umgesetzt werden kann und aus den Materialien neue Zellen entstehen können, ist das Ziel der Forschungsarbeiten. Die Forscher des Circularlab wollen vor allem einen geschlossenen Kreislauf von Batteriematerialien erreichen und damit Nachhaltigkeit sowie Unabhängigkeit von kritischen Rohstoffen sicherstellen.
Am Ende sollen eine ressourcenschonende Elektroden- und Zellproduktion sowie ein effizientes Recycling stehen. Dazu werden bestehende Produktionsprozesse zur Elektrodenfertigung, wie Trocknungstechnologien, im Pilotmaßstab untersucht und optimiert. Das Forschungszentrum Battery Labfactory Braunschweig (BLB) bildet mit seinen jetzt drei Forschungseinrichtungen Productionlab, Circularlab und Diagnosislab einen Großteil des Lebenszyklus und der zirkulären Produktion von Lithiumbatterien in den unterschiedlichen Lebensphasen ab. Das Cicularlab hat Ende 2023 offiziell den Betrieb aufgenommen.
https://www.tu-braunschweig.de/blb
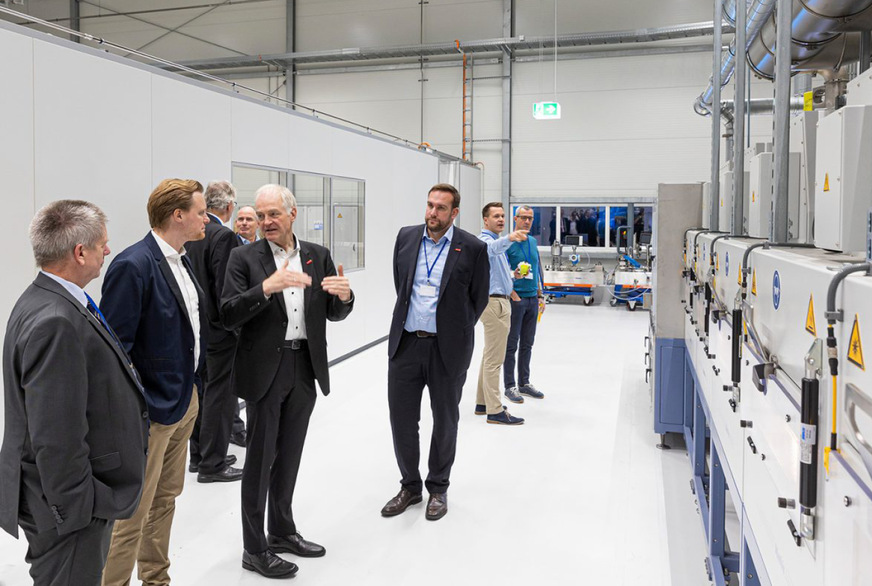
Foto: Christian Bierwagen, TU Braunschweig.