Photovoltaikfassaden müssen nicht zwingend flach sein. Wie eine dreidimensionale Solarfassade aussehen kann, hat Avancis am neuen DHL-Parkhaus in Leipzig gezeigt. Direkt südlich angrenzend an den Leipziger Flughafen hat die DHL-Gruppe einen neuen Bürokomplex errichtet.
Das architektonische Ausrufezeichen des nachhaltigen Campus ist aber ausgerechnet das Parkhaus. Denn es steht direkt an der angrenzenden Bundesstraße 6 und sorgt für weniger Verkehrslärm in den dahinterliegenden Bürogebäuden. Die direkte Ausrichtung der Längsseite des Parkhauses nach Süden ist perfekt geeignet für die Nutzung der Fassade für die Solarenergie.
Kosten im Zaum halten
Es ist aber nicht irgendeine Solarfassade geworden. Vielmehr hat der BIPV-Anbieter Avancis aus Torgau eine wellenförmige Photovoltaikfassade geplant und umgesetzt. Dazu klebt Avancis auf die Rückseite der Module eine spezielle Unterkonstruktion. Damit können die Paneele direkt auf die vertikalen Träger, die eigentliche Anbindung an die Fassade, geschraubt werden.
Avancis hat für das Projekt Solarmodule mit einer Gesamtfläche von 1.872 Quadratmetern produziert. Die Aufgabe war es aber, eine Balance zwischen Ästhetik und technischen Anforderungen zu finden. Denn einerseits sollten sich die Module perfekt in die wellenförmige Struktur der Fassade einpassen. Andererseits sollten die Kosten nicht zu hoch werden. Avancis bietet mit der Modulreihe Skala Paneele in Standardgrößen und mit verschiedenen Farben an. Jede Abweichung sowohl von der Größe als auch von den Farben, die die Torgauer im Portfolio haben, ist mit zusätzlichen Investitionskosten verbunden.
Auf gekrümmten Oberflächen installieren
So war der erste Schritt bei der Auslegung der Fassade die Simulation des potenziellen Energieertrags. Hier waren die Bereiche mit der höchsten Sonneneinstrahlung sowie diverse Verschattungen wichtig. Dies musste aber auch noch mit ästhetischen Vorgaben verknüpft werden. Aus dieser Simulation konnten die Planer bei Avancis die Positionierung und den Anstellwinkel jedes einzelnen Moduls bestimmen, wobei darauf geachtet wurde, dass das Maximum an Solarenergie produziert wird.
Dazu nutzt Avancis computergestützte Planungsalgorithmen. Diese ermöglichen die nahtlose Installation auf gekrümmten Oberflächen, einschließlich freier Formen wie gewellten, gebogenen und kugelförmigen Fassaden. Selbst Fassaden mit facettierten scharfen Kanten. „Unser primäres Ziel ist es dabei, visuell ansprechende Installationen von Skalamodulen zu schaffen und dabei eine optimale Sonneneinstrahlung sicherzustellen – ein entscheidender Aspekt bei der Gestaltung von Solargebäudehüllen“, betont Melicia Planchart, Architektin und Leiterin der Abteilung Digitales Design bei Avancis.
Suchalgorithmus entwickelt
Danach ging es an die Optimierung des Fassadendesigns, also der Unterkonstruktion und der Größe der Solarmodule. „Wir versuchen dabei, die optimale Anzahl verschiedener Elemente für die Unterkonstruktion und die solare Gebäudehülle zu bestimmen“, erklärt Melicia Planchart. Dabei geht es darum, die Anzahl unterschiedlicher Modulgrößen so weit wie möglich zu reduzieren, um möglichst viele Paneele von immer der gleichen Größe in die Fassade zu integrieren.
Bei der Optimierung werden Module mit weniger als fünf Millimeter Größenunterschied zu einer Gruppe zusammengefasst. Dazu nutzt Avancis einen selbst entwickelten Such- und Ersetzungsalgorithmus. „Im ersten Schritt priorisieren wir dabei die verwendeten Standardgrößen, die Avancis ohnehin schon in Serie fertigt“, sagt Melicia Planchart. „Der Algorithmus tauscht im zweiten Schritt systematisch kürzere maßgeschneiderte Module aus, um eine möglichst große Einheitlichkeit zu gewährleisten und die Produktion der Module zu vereinfachen.“
43 Modulgrößen ausgesondert
Auf diese Weise kann Avancis von den Kostenvorteilen einer Produktion von Standardmodulen profitieren und die höheren Kosten für die Herstellung von kürzeren Modulen reduzieren. Am Ende der gesamten Optimierung hat der Such- und Austauschalgorithmus dafür gesorgt, dass von den 109 verschiedenen Modulgrößen, die anfangs berechnet wurden, am Ende noch 66 verschiedene Modulgrößen übrig blieben. Es konnten 43 speziell angefertigte Größen ausgesondert werden. Das betraf etwa 400 Module, die weniger in unterschiedlichen Größen hergestellt werden mussten.
Außerdem haben die Planer einen Algorithmus zur Formfindung eingesetzt. Dieser hat sie dabei unterstützt, die Wellenform aus dem ursprünglichen Projektentwurf des Architekten zu erreichen. „Dabei haben wir die optimale Anzahl von Paneelen, den richtigen Abstand zwischen ihnen für eine belüftete Fassade sowie die passende Ausrichtung zur Sonne berücksichtigt, um den Energieertrag zu maximieren und gleichzeitig die Anzahl der nach unten gerichteten Paneele zu minimieren, die weniger Sonnenstrahlen einfangen würden“, erklärt Melicia Planchart.
Farbgebung hat gepasst
Auch bei der Farbgestaltung geht Avancis auf Kundenwünsche ein. In Leipzig wurden verschiedenfarbige Module verwendet, um die Wellenstruktur der Fassade zusätzlich zur Geltung zu bringen. „Die Farben simulieren wir in unseren 3D-Simulationen“, erklärt Melicia Planchart. „Doch der samtige Effekt der Moduloberfläche ist ein Ergebnis der Farbtechnologie von Avancis. Für das Gebäude waren wir uns sicher, dass die Farbgebung mit der Wellenform hervorragend zur Geltung kommt.“
Eine große Herausforderung war die zeitliche Umsetzung des Projekts. Denn der gesamte Gebäudekomplex inklusive Parkhaus sollte innerhalb von 2,5 Jahren fertiggestellt sein. Um die Solarfassade möglichst schnell zu installieren, hat Avancis ein eigenes Logistikkonzept entwickelt, das einem Ladengeschäft ähnelt.
Logistik optimiert
Jedes Modul wurde mit Größe, Farbe und Position in der Fassade gekennzeichnet. Damit die Monteure auf der Baustelle nicht durcheinanderkommen oder lange suchen müssen, hat sich die Logistik an den vertikalen Trägern orientiert, an denen die Module angeschraubt werden. Jeder Träger bekam eine gesonderte Bezeichnung. Im Lager in Torgau wurden die Module so gepackt, dass jeweils alle Paneele, die an einem vertikalen Träger befestigt werden sollten, zusammen in jeweils einer separaten Kiste landeten.
So mussten die Monteure nur noch die Kiste mit Modulen passend zum jeweiligen vertikalen Träger öffnen und die Paneele dann in der vorgepackten Reihenfolge daran anschrauben. „Was im Nachhinein naheliegend erscheinen mag, erwies sich als zeitsparende und klarere Lösung, die sogar die Effizienz bei der Montage kleinerer und weniger komplexer Projekte übertraf“, berichtet Melicia Planchart.
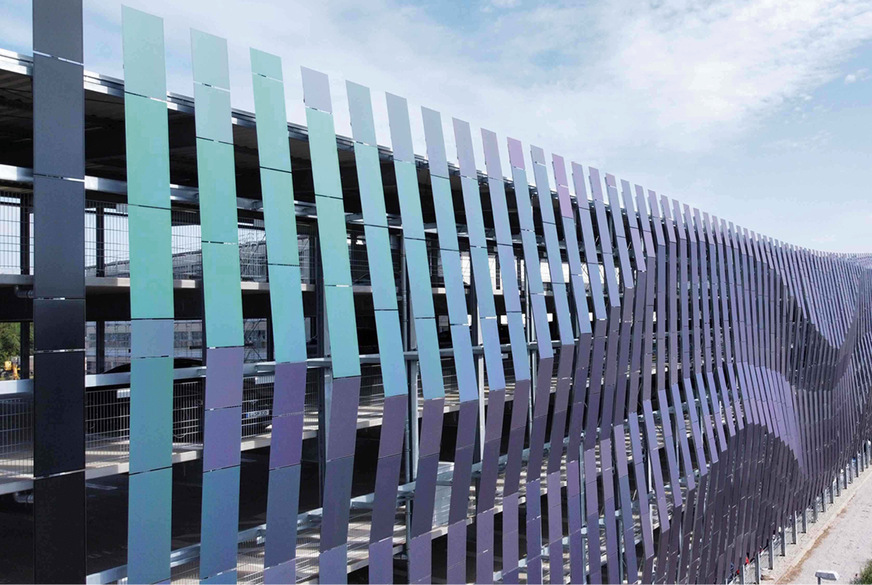
Foto: Avancis