Es ist ein Gewerbebau, wie er in vielen Gewerbegebieten steht. Der nagelneue Anbau zeigt aber, wohin die Reise hier geht: in Richtung Wachstum. Denn in dem Gebäude in Český Krumlov, einem kleinen Ort südlich von České Budějovice, fertigt der Wechselrichterhersteller Fronius die Herzen seiner Geräte. Auf den einzelnen Produktionsinseln wickeln, isolieren und löten schon seit 2009 die Mitarbeiter und Mitarbeiterinnen Spulen und stellen induktive Komponenten unter anderem für die Wechselrichter von Fronius her.
Die Produktionsstätte von Fronius in Český Krumlov existiert aber schon seit Anfang der 1990er-Jahre. Damals hat das österreichische Unternehmen damit begonnen, hier Schweißgeräte herzustellen.
Verschiedene Spulen und Transformatoren
Dazu gehörte auch die Produktion von Transformatoren, die in diese Geräte integriert wurden. „Deshalb hatten wir in Český Krumlov schon immer die Kompetenz für die Fertigung von induktiven Komponenten. Mit der Verlagerung der Schweißgeräteproduktion ins niederösterreichische Sattledt hat sich die Unternehmensleitung entschlossen, die Trafofertigung auch für alle anderen Geschäftsbereiche von Fronius in Český Krumlov zu konzentrieren“, erinnert sich Boris Grbeša, Geschäftsführer der tschechischen Tochtergesellschaft von Fronius.
Kupferband auf Schnittbandkerne
Selbst die Kabel für die Anschlüsse der induktiven Komponenten, die in den Geräten des Unternehmens dafür sorgen, dass Gleichstrom in Wechselstrom gewandelt wird, werden in dem Werk in Český Krumlov konfektioniert. Für die unterschiedlichen Wechselrichtergenerationen und Geschäftssegmente werden verschiedene Drosseln und Trafos gewickelt.
So werden die Drosseln für die bewährten Snapinverter sowie für den Fronius Tauro, der im gewerblichen Segment zum Einsatz kommt, mit einem Kupferband auf Schnittbandkerne gewickelt. Die induktiven Komponenten der neuen Gen24-Generation basieren hingegen auf ringförmigen Kernen, sogenannten Toroiden.
Diese bestehen aus einem runden Ferritkern, um den Kupferdraht gewickelt wird. Je nach Produkt müssen fünf bis acht solcher induktiver Komponenten in einem Wechselrichter eingebaut werden.
Neben der Umwandlung des Stroms in die gewünschte sinusförmige Wechselstromkurve sorgen induktive Komponenten auch für die Sicherheit des Netzes und des Wechselrichters selbst. „Beim Umwandeln des Gleichstroms aus der Solaranlage in Wechselstrom muss die Gleichspannung getaktet werden“, erklärt Boris Grbeša. „Sie wird dann so wieder zusammengesetzt, dass sie die geforderte Sinusform der Wechselspannung bildet.“
Bei diesen Schaltvorgängen entstehen Stufen, die geglättet werden müssen. Um die Spannung zu glätten, werden Kondensatoren verwendet. „Im Fall einer vorübergehenden Netzschwankung trägt die in den induktiven Komponenten gespeicherte Energie zur schnellen Netzstützung bei“, ergänzt Martin Hackl, Leiter der Solarsparte bei Fronius. „Zudem entkoppeln die induktiven Komponenten die Leistungselektronik vom Netz und schützen so den Wechselrichter.“
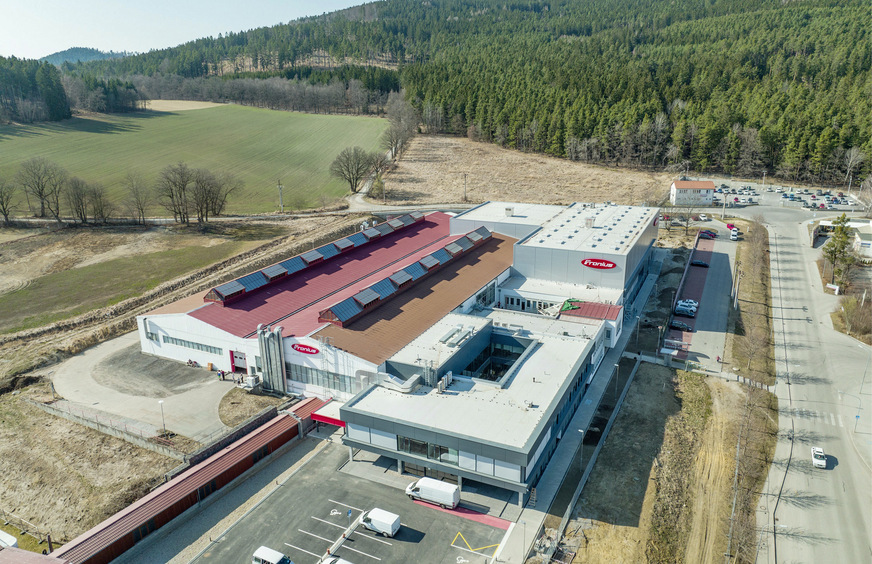
Foto: Fronius International
Hohe Stromqualität sichern
Die induktiven Komponenten haben aber auch eine Filterfunktion. „Denn der Wechselrichter muss mit einer bestimmten Sinusqualität einspeisen", weiß Hackl. „Jede Wechselstromkurve, die wir mit dem Wechselrichter erzeugen, besteht aus einer Grundwelle und Oberwellen. Oberwellen wollen die Netzbetreiber aber vermeiden – ebenso Nachbarn, deren Geräte dadurch gestört werden“, ergänzt Boris Grbeša. „Deshalb gibt es konkrete Standards, welche Oberwellen in welchem Maß man ins Netz schicken darf. Mit entsprechend sorgfältig ausgelegten induktiven Komponenten halten wir diese Standards ein“, sagt Martin Hackl.
Die Produktion der induktiven Komponenten in Český Krumlov ist in Form von Inseln organisiert. Jede dieser Inseln ist eine eigene Produktionslinie, auf der die Mitarbeiter und Mitarbeiterinnen zunächst Kupfer um einen Kern aus Magnetmaterial, zum Beispiel Ferrit, wickeln – jeweils in der vorgesehenen Länge. Sie schirmen die einzelnen Kupferschichten mit Isoliermaterial ab.
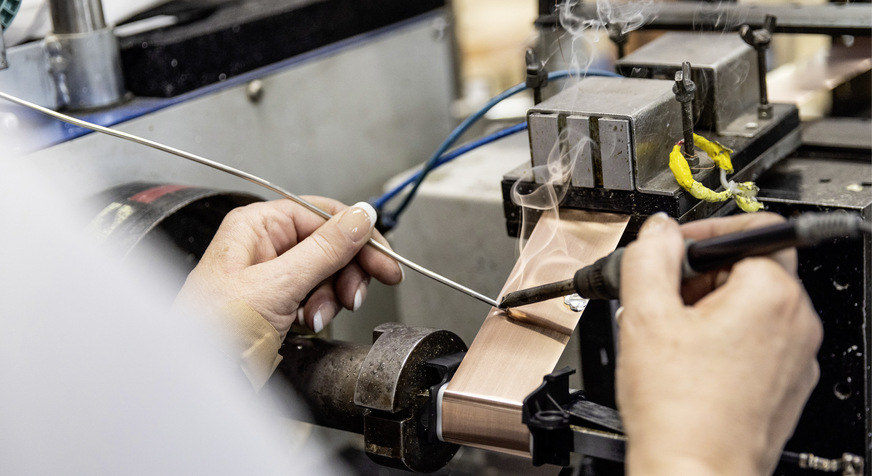
Foto: Fronius International
Kontrolle von Anfang bis Ende
Auf die so entstandene Spule wird ein QR-Code aufgedruckt, der zu einer Datenbank führt, in der sämtliche Werte hinterlegt sind. Hier werden neben dem Produktionsdatum und der Insel, auf der sie hergestellt wird, auch sämtliche Ergebnisse der Qualitäts- und Funktionskontrollen festgehalten. Die erste Qualitätskontrolle erfolgt schon nach dem Wickeln, und nach jedem weiteren Prozessschritt wird wieder kontrolliert.
Auf diese Weise kann Fronius für jeden einzelnen Wechselrichter nachvollziehen, welche individuellen Spulen in ihm verbaut wurden. Dies gibt Fronius aber auch die Möglichkeit, noch während der Produktion der einzelnen induktiven Komponenten zu reagieren, falls sich doch ein Fehler einschleichen sollte.
Für ruhigen Lauf gesorgt
Denn am Ende werden die induktiven Komponenten vergossen. Dann ist kein Eingreifen mehr möglich. Das Vergießen wiederum ist essenziell für die geringe Geräuschentwicklung der Wechselrichter. „Denn mit steigenden Strömen und steigender Frequenz des Stroms können die induktiven Komponenten beginnen zu vibrieren. Das Vergießen ist daher eine wichtige Akustikmaßnahme“, erklärt Martin Hackl.
Um dies zu verhindern, werden die induktiven Komponenten für die Snapinverter in einen speziellen Lack getaucht. Dieser verschließt sämtliche Hohlräume, sodass sich nichts mehr bewegen kann. Danach muss das fertige Bauteil noch für fünf Stunden zum Trocknen in den Ofen.
Retourensystem für Verpackungen
Erst dann kann es verpackt, auf einen Lkw geladen und in das oberösterreichische Sattledt transportiert werden. Dort steht die Produktionshalle von Fronius, in der die einzelnen Teile inklusive der induktiven Komponenten aus Český Krumlov zu Wechselrichtern zusammengebaut werden.
Für die induktiven Komponenten im neuen Gen24 hat sich Fronius etwas anderes einfallen lassen, um die Trockenzeit im Ofen zu vermeiden. Diese werden – nachdem alles fertig montiert und alle Anschlüsse angelötet sind – mit einer speziellen Masse vergossen. Danach müssen sie kurz in eine Vakuumkammer, wo sämtliche Luftblasen entfernt werden, sodass die Vergussmasse in die gesamte induktive Komponente eindringen kann.
Verdopplung alle fünf Jahre
Danach werden die fertigen Bauteile in eine spezielle Verpackung gelegt, bevor sie die Reise nach Sattledt antreten. Unterwegs kann die Vergussmasse aushärten. Dadurch kann das Bauteil aus Český Krumlov, wenn es in Österreich angekommt, gleich in einen Wechselrichter verbaut werden. Die leeren Verpackungen gehen dann wieder retour nach Český Krumlov, wo sie mit neuen induktiven Komponenten befüllt werden.
Die Produktion in Český Krumlov und in Sattledt ist so aufeinander abgestimmt, dass kaum Lagerhaltung notwendig ist. „Wir haben hier nur einen Puffer von ein paar Tagen Produktion. In Sattledt ist ebenfalls noch ein Puffer von ein paar Tagen aufgebaut, sodass es garantiert keinen Stillstand in der Wechselrichterproduktion gibt“, erklärt Boris Grbeša.
Der Bedarf an induktiven Komponenten aus Český Krumlov in Sattledt wächst mit der Nachfrage nach Wechselrichtern von Fronius. „Wir haben unsere Produktionskapazität seit 2009 im Rhythmus von fünf Jahren jeweils verdoppelt und gehen davon aus, dass wir auch in den nächsten fünf Jahren verdoppeln werden“, erklärt Boris Grbeša. Die nächste Erweiterung ist bereits in Planung, obwohl der jüngste Anbau gerade erst fertig geworden ist. Ziel ist es, bis zum Winter 2023 mit dem Bau zu beginnen.
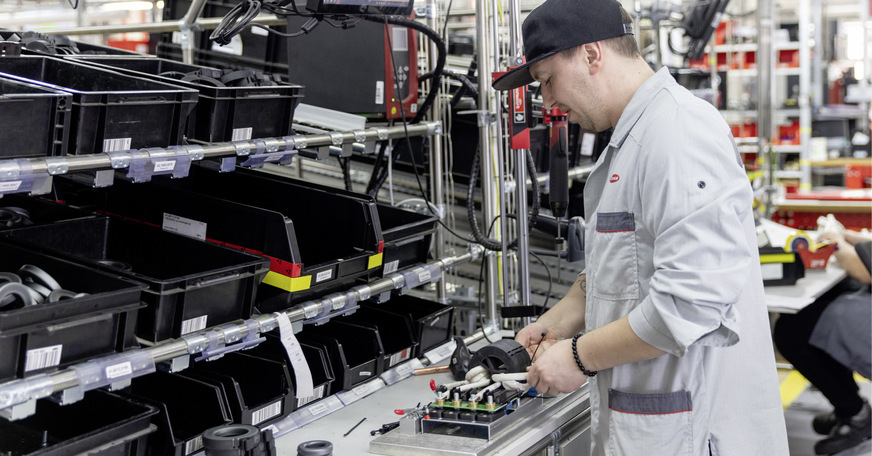
Foto: Fronius International
Wertschöpfung vor Ort
Entsprechend wird sich auch die Zahl der Mitarbeiter in Český Krumlov erhöhen. Derzeit sind hier etwa 500 Mitarbeiter in der Produktion mit der Herstellung der induktiven Komponenten für Wechselrichter, Schweiß- und Ladegeräte sowie von Kabeln beschäftigt. Boris Grbeša rechnet damit, dass es in absehbarer Zeit 1.200 bis 1.300 Mitarbeiter sein werden. Das wird nicht ganz einfach sein, denn auch in der Tschechischen Republik sind Fachkräfte rar gesät und eine großflächige Automatisierung ist nicht einfach umzusetzen.
Dennoch kommt für Fronius die Auslagerung der Herstellung der induktiven Komponenten nicht in Betracht. Das hat gleich mehrere Gründe. „Wir versuchen, unsere Produkte mit viel lokaler Wertschöpfung und den höchsten sozialen Standards herzustellen. Möglichst viele Komponenten für die Geräte beziehen wir aus unserer Umgebung“, erklärt Martin Hackl. „Es ist auch Teil der Verantwortung, die wir als Fronius übernehmen – für die Leute hier und den Standort. Das ist Teil unseres Markenkerns, dem wir treu bleiben. Wir merken auch, dass das zunehmend von den Kunden auch so gewünscht und nachgefragt wird.“
Es ist für viele Kunden von Fronius wichtig, dass die Wertschöpfung vor Ort bleibt und die Wechselrichter nicht einfach aus Baugruppen zusammengeschraubt werden, die vorher um die halbe Welt gereist sind. Für Fronius ist die Produktion in Český Krumlov aber nicht nur aus Nachhaltigkeits- und Verantwortungsgründen wichtig.
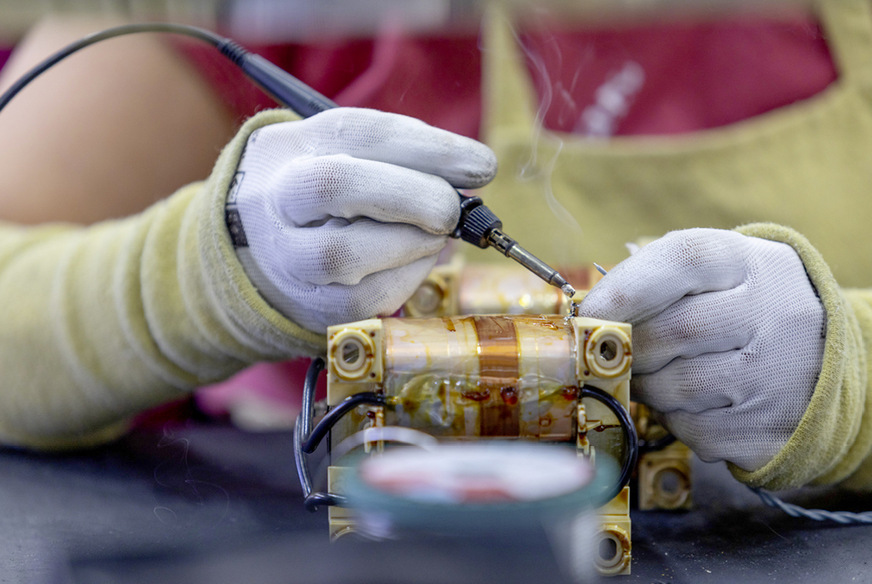
Foto: Fronius International
Mit anderen konkurrenzfähig
In jüngster Zeit wird auch immer deutlicher, dass die Produktionssicherung zunehmend gegenüber den niedrigen Arbeitskosten an Bedeutung gewinnt. „Natürlich müssen wir uns hier aufgrund der Arbeitskosten Gedanken machen, wie wir eine Fertigung von Produkten wie induktiven Komponenten und Kabelbäumen in Europa sichern können. Doch damit haben wir die volle Kontrolle über die technische Entwicklung und die Optimierung. Zumal es auch im Bereich der Automatisierung immer mehr Möglichkeiten geben wird“, sagt Martin Hackl. „Zudem sind wir konkurrenzfähig zu anderen Anbietern, die die Fertigung von induktiven Komponenten als Hauptgeschäft betreiben“, ergänzt Boris Grbeša. Auf diese Hersteller will man sich bei Fronius nicht verlassen müssen.
Zumal das Unternehmen so nicht auf die mühevolle Suche nach Drittanbietern bei der Weiterentwicklung der Wechselrichter angewiesen ist. „Es ist aus der Perspektive der technischen Entwicklung sehr praktisch, wenn wir die induktiven Komponenten beispielsweise auf ein bestimmtes Platzangebot im Wechselrichter auslegen können“, erklärt Martin Hackl. „Wir sind sehr froh, dass wir die Profis auf diesem Gebiet im eigenen Haus haben, mit denen wir ganz konkret diese Lösungen erarbeiten können. Wenn wir auf andere Anbieter zurückgreifen müssten, wären wir entweder in einer viel längeren Entwicklungskette drin oder wir müssten auf Standardkomponenten zurückgreifen und unsere Geräte daraufhin entwickeln.
Lieferkette stabilisieren
Tatsächlich kann Fronius genau diesen Vorteil gut nutzen. Denn die Entwicklung der Wechselrichter passiert in Österreich. Dort kümmert sich die Entwicklungsabteilung auch darum, die dazu passenden induktiven Komponenten auszulegen. Danach übergeben die Entwickler in Österreich die Spezifikationen für die Drosseln, Filter und Trafos an die Produktion in Český Krumlov, wo die Prozesstechnik die entsprechenden Fertigungslinien definiert.
So kann Fronius auf individuelle Lösungen zurückgreifen, was wichtig ist, um technisch wettbewerbsfähig zu bleiben, aber auch um an der Kostenoptimierung zu arbeiten. Selbst für den Fall, dass ein Wechselrichter an die derzeitigen Lieferketten für Halbleiterbauelemente angepasst werden muss, geht das mit der eigenen Fertigung der induktiven Komponenten in Český Krumlov viel schneller. Deshalb ist für Fronius die Kontrolle über die Produktion, Entwicklung und Qualität der für den Wechselrichter so notwendigen induktiven Komponenten ein zentraler Bestandteil des gesamten Produkts. Außerdem sorgt Fronius mit der eigenen Produktion dieser Drosseln und Trafos in Český Krumlov dafür, dass die Lieferketten zumindest in diesem Bereich stabil bleiben.