Nicht nur Lüfter und Relais haben einen hohen Verschleiß. Häufig sind es gerade auch Elektrolytkondensatoren, die besonders schnell den Geist aufgeben. „Hier tauschen wir im Fehlerfall alle Kondensatoren präventiv mit aus, um die Funktionalität des Wechselrichters langfristig zu gewährleisten“, sagt Frederik Bartsch, Key-Account-Manager BVS. Die Techniker der Firma haben bereits einige Geräte aus dem Feld in der Werkstatt inspiziert. Auch Bipolartransistoren, kurz IGBTs, erreichen häufig eine Alterungsschwachstelle, die BVS durch eine komplexe Degradationsmessung feststellen kann. Bei Bedarf werden die IGBTs dann getauscht.
Service bei BVS ab zehn Kilowatt
Parallel zu der bestehenden Industrie-Elektronik-Sparte hat sich die Firma BVS Electronics aus Hanau auf gewerblich genutzte String- und Zentralwechselrichter ab einer Leistung von zehn Kilowatt spezialisiert. BVS überholt und wartet also Wechselrichter. Die sogenannte Produktüberholung umfasst eine vollumfängliche Reinigung des Wechselrichters. „Dabei wird der Wechselrichter, je nach Gerät, auseinandergebaut und die Komponenten werden in einem Ultraschallbad und in einer Industriereinigungsmaschine gesäubert“, erklärt Bartsch. Teilweise werden bei starker Verschmutzung auch händische Reinigungsschritte vorgenommen.
Anschließend werden die Komponenten in einer Trocknungskammer vollständig getrocknet. Im nächsten Schritt finden Vortests statt, um das Fehlerbild zu analysieren. „Im Rahmen der Behebung eines Fehlerbildes werden zusätzlich auch präventiv alle Komponenten mit nutzungs- oder alterungsbedingtem Verschleiß ausgetauscht“, betont Bartsch. Hierbei verwendet BVS Original- oder gleichwertig freigegebene Komponenten.
Tests unter Last im Labor
Nach den produktüberholenden Maßnahmen durchläuft der Wechselrichter noch alle nötigen Funktions- und Lasttests. Hierbei setzt BVS auf eigens entwickelte Testsysteme, die die Funktionalität unter realen Bedingungen prüfen. „Hat der Wechselrichter alle Tests erfolgreich bestanden, wird er zur Auslieferung an den Kunden fertiggestellt und an die Logistik übergeben“, erklärt Bartsch. Der Kunde erhält auf das gesamte Gerät eine 24-monatige Gewährleistung. BVS arbeitet nach den aktuellen Richtlinien – und ist nach DIN EN ISO 9001:2015 und 14001:2015 zertifiziert.
Für die Wartung und Überholung können nicht nur aktuelle Geräte, sondern auch bereits abgekündigte Modelle eingeschickt werden. Produkte, die die Werkstatt regelmäßig durchlaufen, kommen beispielsweise von Fimer ABB Power-One, Danfoss, SMA, Fronius, Kaco New Energy, Kostal, Refusol und Solarmax. Für die Einschübe der Zentralwechselrichter von Fimer ABB Power-One bietet BVS ebenfalls eine volle Produktüberholung an.
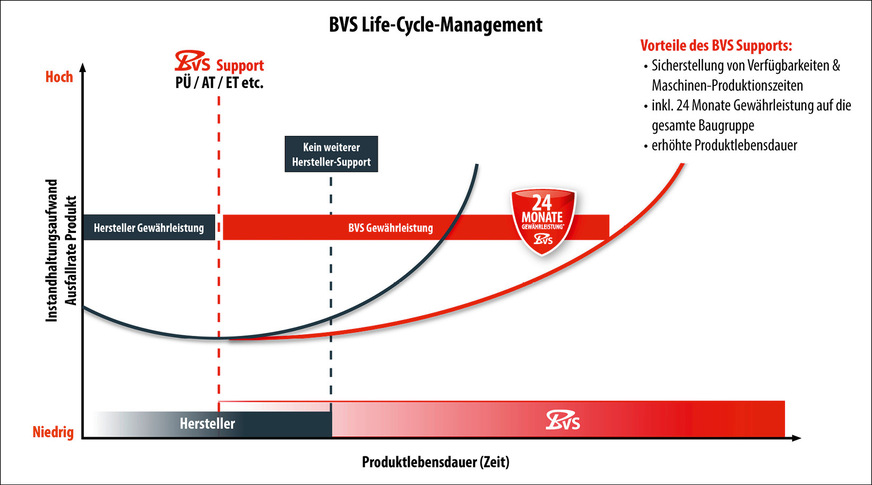
Grafi: BVS
Ausfall nach neun bis zwölf Jahren
Wann sich eine Wartung für die Kunden auszahlt, ist pauschal nicht zu sagen. Produktseitig sei der aktuelle Servicesupport durch den Hersteller zu prüfen, sagt Bartsch. Dabei komme es auf verschiedene Parameter an: beispielsweise ob ein Neugerät überhaupt verfügbar ist, also die Geräteserie überhaupt noch angeboten wird. Zum anderen müsse beachtet werden, ob ein Gerät aus einer neuen Geräteserie oder gar von einem Fremdhersteller mit der Anlage überhaupt kompatibel wäre, was die Kommunikation, die Eingangsspannungen und die Stringbelegungen betrifft. „In vielen Fällen ist dies nicht der Fall und es bleibt nur noch die Alternative eines teuren Repowerings oder Revampings, wogegen im Vergleich eine Reparatur der einzelnen Geräte oftmals die kostengünstigste und nachhaltigste Lösung ist“, erläutert er.
Um unabhängig von der zuvor beschriebenen Betrachtung auf Produktebene die günstigere Lösung zu quantifizieren, müssten verschiedene Punkte beachtet werden, sagt der BVS-Manager. „Grundsätzlich ist es so, dass ein Wechselrichter erfahrungsgemäß nach etwa neun bis zwölf Jahren ausfällt – und mit steigendem Alter der Baugruppe steigt die Ausfallwahrscheinlichkeit sogar exponentiell“, weiß Bartsch aus Erfahrung. Das zeigt auch die Grafik der Badewannenkurve, die den Lebenszyklus von Leistungselektronik und die zunehmende Ausfallwahrscheinlichkeit zeigt.
Bei der Rechnung sind Neuanschaffungskosten inklusive Bevorratungskosten und Kapitalbindung sowie die präventiven Wartungskosten – je nach Baugruppe etwa 40 bis 60 Prozent des Neupreises eines Wechselrichters – den Ausfall- und Ausfallfolgekosten gegenüberzustellen. Häufig fällt diese Rechnung zugunsten der präventiven Wartung des Wechselrichters aus – die meist in den Wintermonaten durchgeführt wird. „Um dauerhaft eine langfristige Laufleistung zu gewährleisten, bieten wir auch präventive Wartungsangebote für alle Wechselrichter einer Solaranlage an, das sogenannte Eco-Vamping“, sagt Bartsch. Das ist eine geplante Produktüberholung aller Wechselrichter eines Solarparks, der in der Zwischenzeit meist Modernisierungs- oder Wartungsarbeiten unterliegt. Um bei der späteren Inbetriebnahme eine langfristige Laufleistung sicherzustellen, sollten auch elektronische Baugruppen wie der Wechselrichter die Pause nutzen, um qualitativ hochwertig überholt zu werden.
Hilker Repair: Pool von 500 Tauschgeräten
Auch die Firma Hilker aus Nordrhein-Westfalen repariert Wechselrichter. „Nach Eingang des Wechselrichters bei uns dauert die Prüfung in der Regel fünf Werktage. Anschließend erhält der Kunde einen detaillierten Prüfbericht mit einer Fehleranalyse und einer Kostenaufstellung für die Reparatur“, beschreibt Marco Thesing den Ablauf. Er ist Vertriebsleiter bei Hilker Repair für den Bereich Instandhaltung und Reparatur von Wechselrichtern und Leistungselektronik.
Der Austauschpool der Firma umfasst rund 500 Geräte von namhaften Herstellern. Hilker verfügt über eine Übersicht der String- oder Zentralwechselrichter, bei denen eine hohe Reparaturquote erzielt wird. Dazu zählen Modelle nahezu aller bekannten Hersteller wie etwa SMA, Fimer, ABB, Delta sowie Fronius, Huawei und Kaco. Bei kleineren Geräten, etwa unter fünf Kilowatt Leistung, lohne sich eine Reparatur in der Regel nicht, da der Kostenunterschied zum Neugerät gering sei, erklärt Thesing. Anders verhält es sich bei Wechselrichtern, deren Austausch technische Anpassungen an der Anlage erfordern würde – etwa bei der Kommunikation oder bei Trafo-Umrichtern, die mit Dünnschichtmodulen genutzt werden.
Zwei Beispielrechnungen für Reparaturkosten
Beim Sungrow SG60KTL liegen die Reparaturkosten bei rund 1.100 Euro netto. Ein Neugerät kostet an die 2.300 Euro netto bei zehn Kilowatt weniger Leistung. Bei Großanlagen verursacht die Kompatibilität der Datenüberwachung und die Anpassung der Zertifizierung weitere Mehrkosten.
Thesing gibt ein zweites konkretes Beispiel: Die Reparaturkosten für den SMA STP17000TL liegen im Schnitt bei 900 Euro netto. Ein Neugerät, der Nachfolger SMA STP X15, kostet im Schnitt zwischen 1.800 bis 2.000 Euro netto bei zwei Kilowatt weniger Leistung. Zudem muss beachtet werden, dass wenn ein weiterer Wechselrichter aus der alten Serie verbaut ist, die Einbindung in die Kommunikation sowie der Regelungstechnik zu Problemen führen kann.
Insgesamt ist die Nachfrage nach Reparaturen in den vergangenen Jahren stark gestiegen. Insbesondere während der Coronapandemie kam es aufgrund von Lieferengpässen zu einer Produktknappheit. „In dieser Phase konnten wir mit unserer schnellen Bearbeitungszeit überzeugen. Zudem fokussieren sich insbesondere asiatische Hersteller weniger auf den Bereich After-Sales-Service“, berichtet Thesing. Ende 2024 sanken die Neupreise durch Überproduktion und volle Lagerkapazitäten deutlich. Dies sorge aktuell gerade bei kleineren Wechselrichtern für weniger Nachfrage. „Wir sehen das jedoch als kurzfristige Sondersituation“, meint er.
https://bvs-electronics.com/de
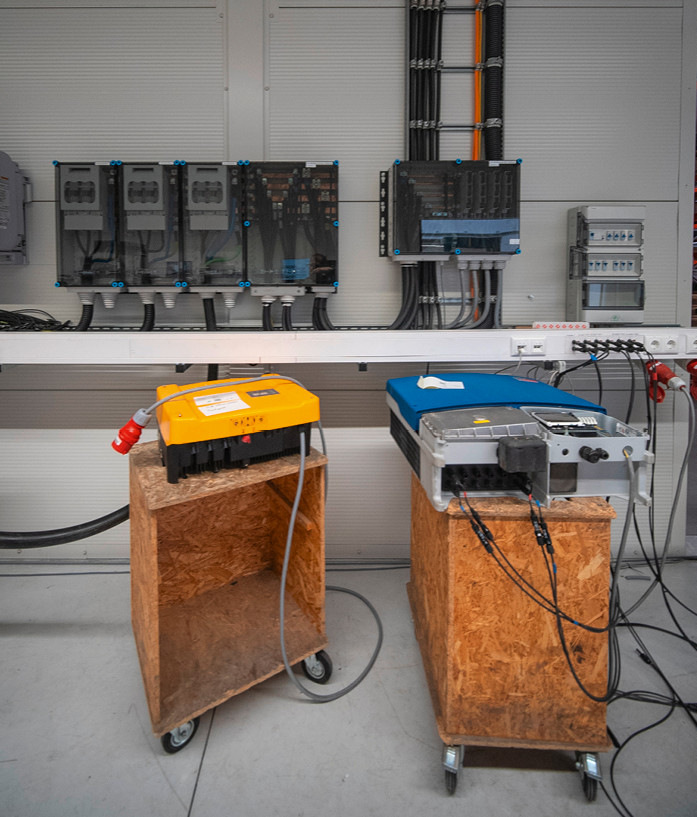
Foto: Hilker Repair
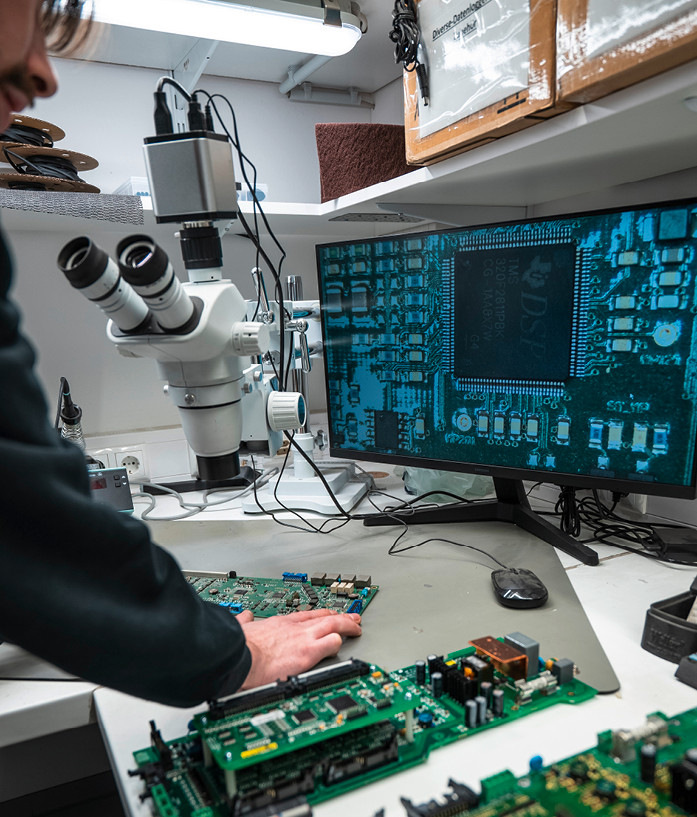
Foto: Hilker Repair
Fraunhofer IMWS
Forscher identifizieren Schwachstellen in Wechselrichtern
Im Projekt Power4re haben die Fraunhofer-Fachleute aus den Felddaten- und Schadensanalysen relevante Schwachstellen identifiziert. Sie haben neue Erkenntnisse bei der Fehleranalyse an Leistungsmodulen verschiedener Leistungsklassen gewonnen.
Innerhalb der drei Jahre umfassenden Projektlaufzeit haben sie ermittelt, welche Faktoren für Defekte verantwortlich sein können, wie sich Schäden sicher erkennen lassen und ab wann sie für die Funktionalität von Bauteilen kritisch werden. Dabei wurden sowohl die Betriebs- und Umgebungsbedingungen von Umrichtern als auch die Materialauswahl und der Aufbau der jeweiligen Komponenten berücksichtigt.
Im nun abgeschlossenen Projekt „Zuverlässige Umrichter für die regenerative Energieversorgung“, kurz Power4re, haben dafür fünf Institute der Fraunhofer-Gesellschaft zusammengearbeitet. „Bei der Optimierung von Wechselrichtern und Frequenzumrichtern reicht es nicht, die Hardware in den Blick zu nehmen und beispielsweise auf Werkstoffe und Verarbeitungsprozesse zu schauen“, berichtet Sandy Klengel. Sie arbeitet als Gruppenleiterin Bewertung elektronischer Systemintegration und Leiterin des Teilprojektes am Fraunhofer IMWS.
Die Herausforderungen reichen demnach von elektrischen Defekten wie Kurzschlüssen über Korrosion und Feuchtebelastung bis zur Delamination und mechanischen Schädigungen.